WELCOME TO RESIDENTIAL AND COMMERCIAL CONCRETE
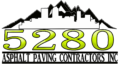
Commercial & Residential Concrete
If you require reliable concrete services, 5280 APC Inc Concrete Services provide you with Residential and Commercial Concrete services for your property. Our concrete contractors will complete your project efficiently and to your satisfaction. We are precise in our measurements and execution, proficient in our craft, and use only the latest technology and tools to provide a completed project that is professional and of high quality. To receive unparalleled concrete Services and concrete removal services for your next project, contact Residential and Commercial call 303 600 8660 today!
HERE’S Info FOR THE PERFECT CONCRETE
5280 asphalt Paving Contractors provide Residential and Commercial Concrete . has a team of professional concrete contractors and masonry contractors serving in Denver metro, and the surrounding areas. We are equipped to handle all your concrete and masonry needs, ensuring that one simple call gets you the service you need. We are committed to ensuring that every aspect of every feature of your exterior works and looks exactly the way you want them to.
Some of our services include:
- Concrete Patios
- Concrete Removal
- Commercial Concrete Services
- Residential Concrete Services
- And More!
We care about our community and hold the deeply ingrained values of integrity, hard work, and fairness. At Residential and Commercial Concrete , we pride ourselves on delivering efficient and affordable assistance, and we are not satisfied until our customers are. Regardless of the task at hand, our professionals will handle the project concerning your preferences, schedule, and budget. For more information about our masonry and concrete services, feel free to contact call us 303 600 8660 for Residential and Commercial Concrete today.
We are a local company based in Denver Metro, we’re dedicated to helping our Colorado customers keep their Concrete looking good for decades. Here are the major types of Concrete maintenance services your trusted 5280 Is asphalt paving company can perform,
Important Notes
Calcium Chloride: Accelerates the hydration process and results in shorter setting times as well as earlier compressive strengths. Calcium chloride is commonly used in cold weather conditions along with hot water provided at the concrete plant. This speeds the finishing process and assists in the removal of forms. It is important to note that calcium chloride is not recommended for use with rebar, metal decking, electrical conduits or metallic based material.
Non-Chloride Accelerator: This is identical to calcium chloride except for the fact that it acts as a non-corrosive accelerator in a liquid. Non-chloride accelerator is also added at the concrete plant.
Retarder: This slows down the hydration process and results in longer setting times. Retarder is commonly used in hot weather conditions as it slows down the finishing process. When the temperature is above 85 degrees or when concrete is being placed in direct sun light in hot weather, the hydration process is greatly accelerated. Retarder helps to slow down the hydration process to provide enough time to place the concrete.
High Range Water Reducer (Superplasticizer): Superplasticizer is a water reducing admixture that is added at the concrete plant. It produces a high slump and increases flowablity. Superplasticizer is commonly used for pumping concrete, high strength concrete and enabling the concrete to flow around rebar and matting. Superplasticizer is useful for getting concrete into tight areas such as corners and turns without using excessive water.
Fibermesh: A polypropylene fiber mesh product added at the concrete plant that eliminates the use of wire mesh. Fiber gives consistent reinforcement throughout the concrete mix. It also reduces the square foot cost for the contractor. Fiber eliminates the labor associated with wire mesh. If fibermesh is not properly placed above the ground with chairs, it will lay on the bottom of the slab instead of in the middle where it needs to be to prevent shrinkage cracks. It should be noted that steel fibers are also available and can increase tensile strength, offer excellent crack control, reduce floor thickness and increase load bearing capacity.
Expansion Joints: A fibrous material that is generally 1/2 inch thick, 10 ft long and range in width from 3″ to 6″. Expansion joints are commonly used to control cracks in slabs, driveways and sidewalks. Expansion joints should be placed 2 feet apart for every inch of thickness of the slab.
Concrete Pumps: Concrete pumps refer to separate trucks that contains a pump, with pipe and hose. Concrete pumps can be used to place concrete in areas that are difficult to reach. Concrete Line Pumps are proven useful when trying to reach areas such as inside homes, back yards and just about any horizontal application up to 300 feet. Concrete Boom Pumps should be used to reach distances greater than 300 feet or for vertical applications such as high rises.
Color: Coloring agents can be added either on the job site or at the concrete plant. Colorin agents come in liquid and powder forms from Davis Colors or L.M. Scofield. There are over 50 colors to choose from. Coloring agents are ideal for driveways, patios, walkways and concrete stamping. Feel free to contact us for availability and color charts.
Fly Ash: Fly ash refers to the finely ground glassy granular material formed of an inorganic residue resulting from coal combustion in modern power plants that burn fossil fuel. Fly ash is considerd a viable pound for pound replacement for cement because it provides improved strength, pumpability and workability. Fly Ash can be used as much as a 30% replacement for cement in a concrete mix design. Fly ash is an environmentally friendly solution.
Ground Granulated Blast Furnace Slag: Finely ground glassy granular material is formed when molten blast-furnace slag is rapidly chilled by the immersion of water. Essentially, blast-furnace slag is comprised of silicates and other bases that is developed into a molten condition simultaneously with iron in a blast-furnace. “Slag” a recycled product is a viable pound for pound replacement for cement. “Slag” is environmentally friendly and provides improved workability, pumpability and finish, along with providing increased compressive and flexural strength. Slag can be used as much as a 50% replacement for cement in a concrete mix design.
To extend the life of your concrete or asphalt pavement, it’s important to get regular maintenance from a trusted local paving company. 5280 Asphalt Paving Contractors Inc is this trusted company. We want our local clients to get the most out of their Concrete sevice, so we offer cost-effective concrete maintenance services designed to rehabilitate and restore Cement at all stages of its life. Will work with you to create a custom ongoing maintenance plan that keeps your flat work Area free of debris and damage and lengthens it’s lifespan by years
- What is the difference between cement and concrete?
Although the terms cement and concrete often are used interchangeably, cement is actually an ingredient of concrete. Concrete is a mixture of aggregates and paste. The aggregates are sand and gravel or crushed stone; the paste is water and portland cement.
Cement comprises from 10 to 15 percent of the concrete mix, by volume. Through a process called hydration, the cement and water harden and bind the aggregates into a rocklike mass. This hardening process continues for years meaning that concrete gets stronger as it gets older.
Portland cement is not a brand name, but the generic term for the type of cement used in virtually all concrete, just as stainless is a type of steel and sterling a type of silver. Therefore, there is no such thing as a cement sidewalk, or a cement mixer; the proper terms are concrete sidewalk and concrete mixer.
- How is portland cement made?
Cement manufacturers mine materials such as limestone, shale, iron ore, and clay, crushed and screened the rock, and place it in a cement kiln. After being heated to extremely high temperatures, these materials form a small ball called “clinker” that is very finely grounded to produce portland cement.
Lime and silica make up about 85 percent of the ingredients of cement. Other elements include alumina and iron oxide. The rotating kiln that cooks the materials resembles a large horizontal pipe with a diameter of 10 to 15 feet and a length of 300 feet or more. One end is raised slightly. The raw mix is placed in the high end and as the kiln rotates the materials move slowly toward the lower end. Flame jets at the lower end heat all the materials in the kiln to high temperatures that range between 2,700 and 3,000 degrees Fahrenheit. This high heat drives off, or calcines, the chemically combined water and carbon dioxide from the raw materials and forms new compounds (tricalcium silicate, dicalcium silicate, tricalcium aluminate and tetracalcium aluminoferrite). For each ton of material that goes into the feed end of the kiln, two thirds of a ton comes out the discharge end, called clinker. This clinker is in the form of marble sized pellets. The clinker is very finely ground to produce portland cement. Manufacturers often add gypsum and/or limestone during the grinding process.
- Are there different types of portland cement?
Though all portland cement is similar, eight types of cement are manufactured to meet different physical and chemical requirements for specific applications:
- Type I is a general purpose portland cement suitable for most uses.
- Type II is used for structures in water or soil containing moderate amounts of sulfate.
- Type II(MH) is a moderately sulfate resistant cement that also generates moderate heat during curing.
- Type III cement provides high strength at an early state, usually in a week or less.
- Type IV moderates heat generated by hydration that is used for massive concrete structures such as dams.
- Type V cement resists chemical attack by soil and water high in sulfates.
- Types IA, IIA, I(MH)A and IIIA are cements used to make air-entrained concrete. They have the same properties as Types I, II, II(MH), and III, except that they have small quantities of air-entraining materials combined with them.
White portland cement is made from the same raw materials as regular portland cement, but containing little or no iron or manganese, the substances that give conventional cement its gray color.
Some portland cements meet requirements for multiple cement types. For example, some cements are sold as Type I/II cements, which means that those cements meet all of the specification requirement in ASTM C150 (or AASHTO M 85) for both Type I and Type II.
See also: What are blended cements?
- What are blended cements?
Blended cements are another type of hydraulic cement like portland cement. Blended hydraulic cements are produced by intergrinding or blending two or more types of fine materials: portland cement and one (or two) of the following: limestone, slag cement, or pozzolans like fly ash, silica fume, or calcined clay. Blended hydraulic cements must conform to the requirements of ASTM C595 (or AASHTO M 240), Standard Specification for Blended Hydraulic Cements. Blended cements are used in all aspects of concrete construction in the same manner as portland cements. Blended cements can be used as the sole cementitious material in concrete or they can be used in combination with other supplementary cementitious materials added at the concrete plant.
ASTM C595 recognizes four classes of blended cements:
- Type IL, Portland-limestone cement
- Type IP, Portland-pozzolan cement
- Type IS, Portland blast-furnace slag cement
- Type IT, Ternary blended cement
Blended cements can be tested to verify special properties like low or moderate heat development, and moderate or high sulfate resistance. If this is the case, suffixes are added to the cement type names: LH, MH, MS, or HS. Air-entraining blended cement can also be produced.
- How do you control the strength of concrete?
The easiest way to add strength is to add cement. The factor that most predominantly influences concrete strength is the ratio of water to cement in the cement paste that binds the aggregates together. The higher this ratio is, the weaker the concrete will be and vice versa. Every desirable physical property that you can measure will be adversely affected by adding more water.
- What is alkali-silica reactivity (ASR)?
Alkali-silica reactivity is an expansive reaction between reactive forms of silica in aggregates and potassium and sodium alkalis, mostly from cement, but also from aggregates, pozzolans, admixtures and mixing water. External sources of alkali from soil, deicers and industrial processes can also contribute to reactivity. The reaction forms an alkali-silica gel that swells as it draws water from the surrounding cement paste, thereby inducing pressure, expansion and cracking of the aggregate and surrounding paste. This often results in map-pattern cracks, sometimes referred to as alligator pattern cracking. ASR can be avoided through 1) proper aggregate selection, 2) use of blended cements, 3) use of proper pozzolanic materials and 4) contaminant-free mixing water.
- How do you protect a concrete surface from aggressive materials like acids?
Many materials have no effect on concrete. However, there are some aggressive materials, such as most acids, that can have a deteriorating effect on concrete. The first line of defense against chemical attack is to use quality concrete with maximum chemical resistance, followed by the application of protective treatments to keep corrosive substances from contacting the concrete. Principles and practices that improve the chemical resistance of concrete include using a low water-cement ratio, selecting a suitable cement type (such as sulfate-resistant cement to prevent sulfate attack), using suitable aggregates, water and air entrainment. A large number of chemical formulations are available as sealers and coatings to protect concrete from a variety of environments; detailed recommendations should be requested from manufacturers, formulators or material suppliers.
- What are the decorative finishes that can be applied to concrete surfaces?
Color may be added to concrete by adding pigments-before or after concrete is place-and using white cement rather than conventional gray cement, by using chemical stains, or by exposing colorful aggregates at the surface. Textured finishes can vary from a smooth polish to the roughness of gravel. Geometric patterns can be scored, stamped, rolled, or inlaid into the concrete to resemble stone, brick or tile paving. Other interesting patterns are obtained by using divider strips (commonly redwood) to form panels of various sizes and shapes rectangular, square, and circular or diamond. Special techniques are available to make concrete slip-resistant and sparkling.
- How do you remove stains from concrete?
Stains can be removed from concrete with dry or mechanical methods, or by wet methods using chemical or water.
Common dry methods include sandblasting, flame cleaning and shot blasting, grinding, scabbing, planning and scouring. Steel-wire brushes should be used with care because they can leave metal particles on the surface that later may rust and stain the concrete.
Wet methods involve the application of water or specific chemicals according to the nature of the stain. The chemical treatment either dissolves the staining substance so it can be blotted up from the surface of the concrete or bleaches the staining substance so it will not show.
- What is 3,000 pound concrete?
It is concrete that is strong enough to carry a compressive stress of 3,000 psi at 28 days. Concrete may be specified at other strengths as well. Conventional concrete has strengths of 7,000 psi or less; concrete with strengths between 7,000 and 14,500 psi is considered high-strength concrete.
- What does 28-day strength mean?
Concrete hardens and gains strength as it hydrates. The hydration process continues over a long period of time. It happens rapidly at first and slows down as time goes by. To measure the ultimate strength of concrete would require a wait of several years. This would be impractical, so a time period of 28 days was selected by specification writing authorities as the age that all concrete should be tested. At this age, a substantial percentage of the hydration has taken place.
- Will concrete harden under water?
Portland cement is a hydraulic cement which means that it sets and hardens due to a chemical reaction with water. Consequently, it will harden under water.
- Why do concrete surfaces flake and spall?
Concrete surfaces can flake or spall for one or more of the following reasons:
- In areas of the country that are subjected to freezing and thawing the concrete should be air-entrained to resist flaking and scaling of the surface. If air-entrained concrete is not used, there will be subsequent damage to the surface
- The water/cement ratio should be as low as possible to improve durability of the surface. Too much water in the mix will produce a weaker, less durable concrete that will contribute to early flaking and spalling of the surface.
- The finishing operations should not begin until the water sheen on the surface is gone and excess bleed water on the surface has had a chance to evaporate. If this excess water is worked into the concrete because the finishing operations are begun too soon, the concrete on the surface will have too high a water content and will be weaker and less durable.
- How can you tell if you’re getting the amount of concrete you’re paying for?
The real indicator is the yield, or the actual volume produced based on the actual batch quantities of cement, water and aggregates. The unit weight test can be used to determine the yield of a sample of the ready mixed concrete as delivered. It’s a simple calculation that requires the unit weight of all materials batched. The total weight information may be shown on the delivery ticket or it can be provided by the producer. Many concrete producers actually over yield by about ½ percent to make sure they aren’t short-changing their customers. But other producers may not even realize that a mix designed for one cubic yard might only produce 26.5 cubic feet or 98 percent of what they designed.
- Why does concrete crack?
Concrete, like all other materials, will slightly change in volume when it dries out. In typical concrete this change amounts to about 500 millionths. Translated into dimensions-this is about 1/16 of an inch in 10 feet. The reason that contractors put joints in concrete pavements and floors is to allow the concrete to crack in a neat, straight line at the joint when the volume of the concrete changes due to shrinkage.
- What are recommended mix proportions for good concrete?
Good concrete can be obtained by using a wide variety of mix proportions if proper mix design procedures are used. A good general rule to use is the rule of 6’s:
- A minimum cement content of six bags per cubic yard of concrete,
- A maximum water content of 6 gallons per bag of cement,
- A curing period (keeping concrete moist) a minimum of six days, and
- An air content of 6 percent (if concrete will be subject to freezing and thawing).
What is “Ready-Mixed” concrete?
Commercial Concrete delivers what is known as Ready-Mixed Concrete. When you place a concrete order, our specialists match your requirements with a specific mix design from our database. The mix ingredients are then sent to batch panels that load all of the raw materials into a drum which mixes the concrete. When the concrete truck arrives at the job site, the product is properly mixed and ready to pour. Each load is custom made to suit the application according to a specific mix design. The customize mix design is put together just moments before the truck leaves for the job site. The batching of the raw materials in their specific quantities is computerized to guarantee accurate combinations and ensure reproducible mixes.
What is concrete used for?
Concrete is considered to be one of the most versatile building materials used in today’s construction. Concrete is used in place of large steel girders and steel decking. Reinforced concrete is used to make building columns and decks in high rises. Concrete is an economical building solution that is increasingly used in today’s construction.
Concrete is extremely versatile and is widely available and can be used in a variety of applications. Concrete is commonly used in large building construction as well as in residential applications for driveways, house foundations, walls and much more.
Concrete is also used for paving, curb and gutter applications. “Precast concrete” is also used to make pre-made molds. Molds are filled with concrete to produce a host of projects such as drainage piping or underground vaults. Tilt-up concrete construction is a building process mainly used in large warehouses with a large flat floor and semi-identical wall sections. Construction crews first pour a large flat floor then spray a non-stick film onto the floor. The wall sections are actually formed on top of the floors and then “tilted up” into place using a crane.
How is the strength of concrete measured?
The reaction between water and cement gives concrete its strength. The important water-to-cement ratio is responsible for the strength of the finished product. Concrete strength is usually measured by its compressive and flexural strength in Pounds per Square Inch (PSI). When you order a “Bag” mix you’re really ordering a specific quantity of cement per cubic yard of concrete. Using some conversion factors you can translate between the two.
It takes time for concrete to achieve its full strength. They say that the innermost concrete poured in the Hoover Dam is still hardening to this day! Often concrete is measured for strength at intervals of 7 days, 14 days, 28 days, and sometimes 56 days. We assume that the 28 day strength test will be an accurate measurement of the final strength of the product.
Your account representative can help you determine what strength of concrete you need. As you can imagine, cement is a costly material in the production of concrete. We tailor specific mixes to specific applications so that you can successfully accomplish the goals of your project in an economical way.
Why would you add ice or hot water to your concrete?
Weather conditions are often the enemy of concrete. Extremely hot dry weather causes concrete to set up very quickly, making it difficult to place and finish. Extremely cold weather can cause the top layer of concrete to freeze and flake off, often ruining hours of hard work and thousands of dollars worth of material. Rain can make concrete difficult to finish as the rain washes away the smooth creamy layer that finishing trowels bring to the surface, exposing the aggregate. That’s a lot to worry about. Thankfully, extra products can help.
Ice: During the summer months you can also substitute ice for a percentage of water in the mix in order to lower the core temperature of the concrete and slow the hydration rate. This helps counteract the effects of the air temperature and the heat contained in the raw materials. Ask your account representative about adding ice to your mix.
Hot Water: During the winter months we substitute regular water with heated water to increase the core temperature of the concrete to prevent freezing and allow more time for the hydration process to take place.
What is air entrained concrete?
Air Entrained Concrete: Concrete inherently contains entrapped air of less than 3% by volume as a result of the mixing process. Air Entraining Admixtures are used to entrain air contents of 4-8% by volume of concrete. Entrained air is necessary to protect concrete that is exposed to freeze/thaw cycles in a saturated state. These microscopic entrained air bubbles capture water and allow it to freeze and thaw without deteriorating the concrete.
What other ‘extra products’ can help me?
Retarder: Retarder is used to decrease the hydration rate of cement, thus giving you or your contractor more time to place and finish our products before the concrete begins to set. Retarder can be well worth your additional investment. It provides an added measure of workability and reduces the rate of heat increase produced by the hydration process. Consider adding retarder on hot, dry days to slow the set rate, allowing for a better finish. Also consider adding retarder if you need more than 30 minutes to unload the truck (i.e. if you’re going to be using buckets or wheelbarrows to transport the concrete from the truck to your work area). By adding retarder to your mix you can expect to retard the set time by 1.5 hours to 8 hours depending on the dosage that you order. You can use retarder for just about any concrete application.
Water Reducers: Water reducers are often used to increase the workability and the strength of concrete. It makes concrete “wetter” without adding water. If you’re pouring plain concrete and find that it’s difficult to place or pump, you may be tempted to ask the driver to add additional water to the mix. Beware that by adding water you could be reducing the compressive strength of the finished product. If, however, you choose to add a water reducer, you can expect a more workable product with the benefit of needing less water to make it “wet”. The result is a high-strength mix that can be pumped at a 4″-6″ slump. You can also achieve a strength gain over traditional concrete when poured at the same slump.
Your account rep can suggest an appropriate dosage if you’re interested in adding water reducer to your mix.
Accelerators: Accelerators are often used in cold weather to speed up the setting time of concrete. In cold weather it’s often helpful to add accelerators to speed up the cement hydration therefore increasing the initial set of the concrete. Always take great care when pouring concrete in cold temperatures. You’re account rep or salesperson can help you determine the appropriate amount of accelerator for your application.
Accelerators can also be used in high-early mixes, or mixes that require high strength in a short amount of time. Concrete contractors on high rise projects often use high-early mixes when pouring columns and decks to produce enough strength in 7 days to pour the next elevated deck and columns rather than waiting for 14 or 28 day compressive strength. This facilitates the rapid building schedules that general contractors often require.